"Wouldn't the hydrostatic pressure be the same regardless? "
The hydrostatic pressure (also known as head) will be the same for any location, supply level relative to the return line /exit. If you have ever used a syphon hose, you will know that if the hose exit is brought up to the same level as the supply (tank) the flow will stop exactly at the level of the supply. If you raise the supply well above the exit, you will get higher pressure.
The only way, that I can think to reduce the head, below that of your wing tanks, is to install a header tank, at a lower position (than wing tanks) in the aircraft/fuselage. Note: the header can not be directly plumbed into the wing tank supply, as you will, in effect, be creating the same head/pressure. The header tank would need to be open to atmosphere ie have a breather.
1. Am I correct in thinking the distance should be measured from the top of the wing tank aka the highest fluid level? CORRECT
2. Would that distance be measured from where the return starts (top of the engine)
The head/pressure will be from the top of the tank fuel level, to the exit point of the return line IF THIS ABOVE FUEL LEVEL .
If the exit point is BELOW FUEL LEVEL ,the head will be between tank full and tank empty. or the lowest point in the return line? INCORRECT. Head is measured as the vertical distance between pump supply & exit - loops/bends etc have nil influence.
3. Any specific place I should port the return line into the header, or just somewhere in the bottom slightly above the outlet? REFERRED TO FORUM CONVERSATION - I preferer to plumb the return, to a low pressure area ie above tank fuel level but this is not absolutely necessary.
4. Do I need a check valve on the return line to prevent flow going back into the regulator when the engine is off? NO - In theory there will be nil flow in any direction when the pump(s) is turned off. If you plumb below the fuel level & have a fuel control valve (OFF/ON) on the main supply, turning OFF will not completely isolate the tank fuel. 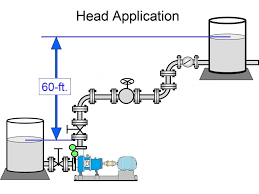